CDSCO License for Polyglyconate suture
Medical Device Information
Intended Use
A sterile, single-strand (monofilament), synthetic, bioabsorbable thread made from polyglyconate (prepared from a copolymer of glycolic acid and trimethylene carbonate) intended to join (approximate) the edges of a soft-tissue wound or incision by stitching or to ligate soft tissues (especially in paediatric cardiovascular surgeries). It may include an attached needle intended to be disposed of after single use. The thread provides extended temporary wound support, until the wound sufficiently heals to withstand normal stress, and is subsequently absorbed by hydrolysis. This is a single-use device.
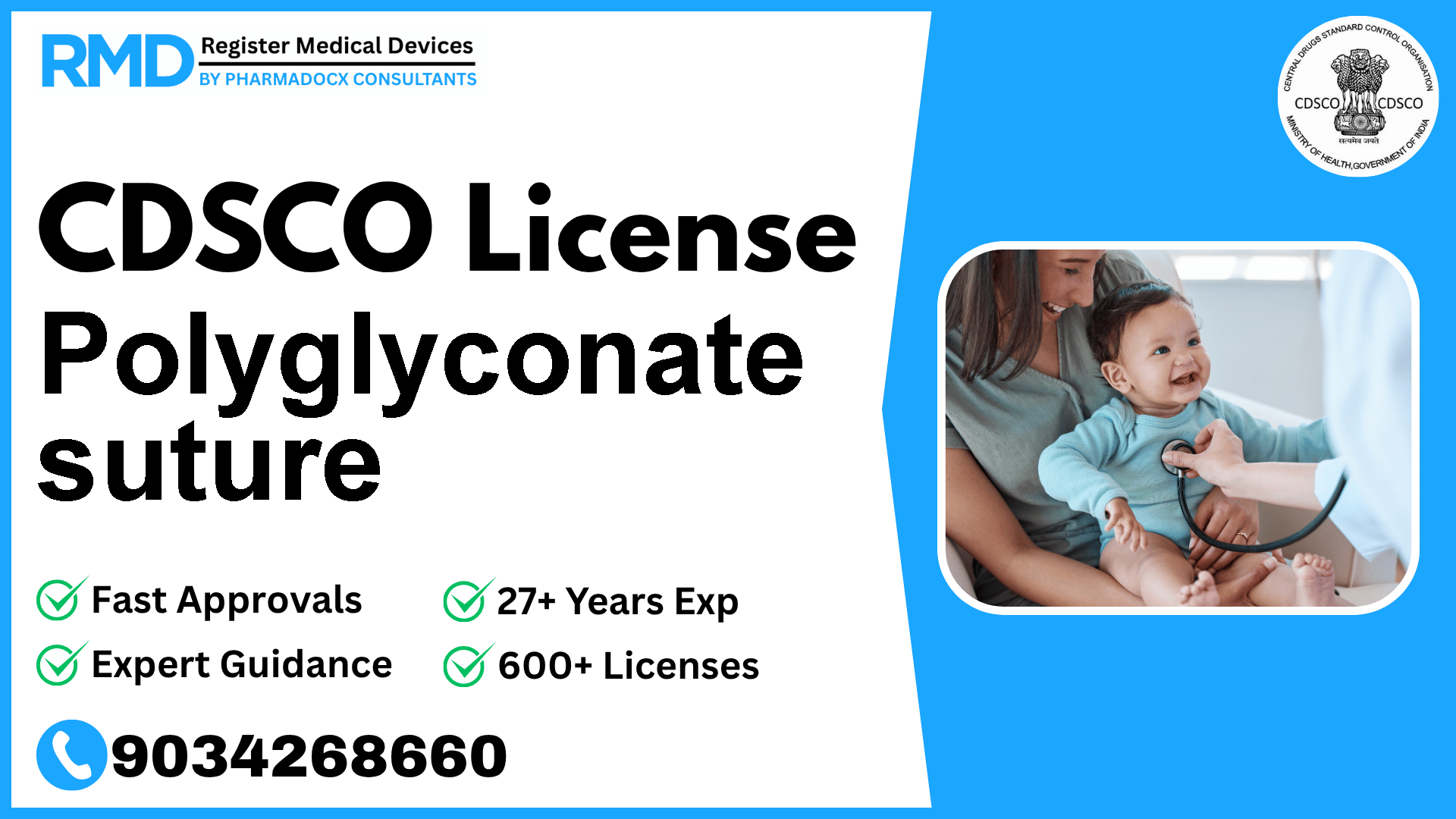
Comprehensive Guide to CDSCO Licensing for Polyglyconate Sutures (Class D Medical Device)
Polyglyconate sutures represent a critical category within pediatric and neonatal surgical care, offering sterile, bioabsorbable support for soft tissue healing. Given their vital role in sensitive surgeries such as pediatric cardiovascular procedures, these devices are classified as Class D under the Indian medical device regulatory framework, reflecting the highest risk category. Navigating the Central Drugs Standard Control Organization (CDSCO) licensing process for such devices requires specialized knowledge, precise documentation, and adherence to strict timelines.
With over 25 years of regulatory consulting experience and having supported more than 500 companies in securing CDSCO licenses, we provide you a detailed, actionable roadmap tailored for Polyglyconate sutures, ensuring a streamlined pathway to market entry in India.
CDSCO Regulatory Framework for Polyglyconate Sutures
In India, medical devices are regulated under the Medical Device Rules (MDR) 2017, administered by CDSCO. Polyglyconate sutures fall under Class D due to their critical use and implantable nature, requiring a rigorous licensing process governed by the Central Licensing Authority.
The device is notified under File No. 29/MiscJ03/2020-DC (150) dated 23.8.2021, confirming its classification and regulatory status. Compliance with this classification ensures patient safety and conformity to national and international standards.
Risk Classification and License Requirements
Polyglyconate sutures, as a Class D device, demand the highest level of regulatory scrutiny:
- Risk Class: D (Highest risk)
- License Type: MD9 Manufacturing License (Form MD7)
- Authority: Central Licensing Authority (CDSCO HQ)
- License for Import: MD15 (Import License, Form MD14)
The MD9 license is mandatory for manufacturing such devices in India, while the MD15 license is essential for importers wishing to bring these sutures into the Indian market.
Manufacturing License Process for Polyglyconate Sutures (MD9)
The manufacturing license (MD9) process for Class D devices like Polyglyconate sutures is comprehensive and involves several critical phases:
Test License Application (Form MD13): Obtain a test license to manufacture the device on a trial basis. This step typically takes 1.5 to 2 months.
Product Testing: Samples must be tested at CDSCO-approved laboratories to validate safety and performance. For guidance on approved labs, visit Testing Laboratories.
Documentation Preparation: Assemble detailed technical files, including Device Master File (DMF), Plant Master File (PMF), risk management documents, and quality management system evidence.
License Application (Form MD7): Submit the formal application for the MD9 manufacturing license.
Inspection and Audit: CDSCO inspectors conduct a thorough audit of manufacturing facilities and documentation.
Query Resolution: Address any observations or queries raised by CDSCO during the inspection.
License Grant: Upon satisfactory compliance, the MD9 license is issued.
For a deeper dive into the MD9 licensing process, refer to our detailed MD9 License Guide.
Essential Documents Required for MD9 Manufacturing License
Successful application hinges on meticulous documentation. Below are the key documents needed for Polyglyconate suture manufacturing:
- Company Constitution: Incorporation certificate, partnership deed, or equivalent.
- Proof of Premises Ownership/Lease Agreement: Valid legal proof ensuring the manufacturing site.
- Technical Staff Details: Qualification and experience certificates of key personnel.
- Fire NOC and Pollution Control NOC: Clearances from relevant authorities.
- Device Master File (DMF): Comprehensive technical documentation covering design, materials, and safety features. Our Device Master File Guide offers practical insights.
- Plant Master File (PMF): Details on manufacturing processes, equipment, quality control, and facilities. Learn how to prepare it easily in our Plant Master File Guide.
- Essential Principles Compliance Checklist: Demonstrating conformity with MDR essential principles.
- Risk Management File: Including risk analysis and mitigation strategies compliant with ISO 14971. For implementing robust risk management, see our Risk Management Guide.
- Test Reports: From CDSCO-approved labs confirming product safety and performance.
- Labels and Instructions for Use (IFU): Clear, compliant labeling and usage instructions.
- Quality Management System (QMS) Documents: Evidence of ISO 13485:2016 certification and internal procedures.
Import License Process for Polyglyconate Sutures (MD15)
For importers, the MD15 license application is directed to the Central Licensing Authority. The process is as follows:
Document Preparation: Compile necessary documents including manufacturing license of the product from the country of origin, Free Sale Certificate, ISO 13485:2016, CE Certificate, Device and Plant Master Files, and wholesale license.
License Application (Form MD14): Submit the application through the CDSCO MD Online Portal.
Review and Queries: The authority reviews the application and may raise queries.
License Grant: Upon satisfactory review, the MD15 import license is granted.
Refer to our Import License Guide for detailed assistance.
Documents Required for MD15 Import License
- Valid manufacturing license of the device from the country of origin
- Free Sale Certificate
- ISO 13485:2016 certificate
- CE Certificate or equivalent
- Device Master File and Plant Master File
- Wholesale drug license
- Company constitution documents
- Proof of payment of government fees
Timeline and Processing Duration
Process Stage | Duration |
---|---|
Test License (MD13) | 1.5 - 2 months |
Product Testing | 1 - 1.5 months |
Document Preparation | 2 - 3 weeks |
MD9 License Application & Audit | 2 months |
Query Resolution & License Grant | 2 - 4 weeks |
Total estimated time: Approximately 4 to 5 months from initial test license application to final MD9 license grant.
For import licenses (MD15), the process usually takes 5 to 6 months.
Government Fees and Costs
License Type | Application Fee | Per Product Fee |
---|---|---|
MD9 Manufacturing | INR 50,000 (~$600) | INR 1,000 (~$12) |
MD15 Import | Class D: INR 2,10,000 (~$3,000 per site) | INR 1,12,500 (~$1,500 per product) |
Additional costs to consider:
- Testing fees at CDSCO-approved labs
- Audit fees for notified bodies or CDSCO inspections
- Consultancy and document preparation fees
Common Challenges and Solutions
Challenge 1: Delays in Product Testing
- Solution: Engage early with CDSCO-approved testing laboratories and submit complete, compliant samples to avoid retesting.
Challenge 2: Incomplete Documentation
- Solution: Use comprehensive checklists and templates for DMF, PMF, and Risk Management Files. Our expert guides can streamline this step.
Challenge 3: Audit Non-Compliance
- Solution: Conduct internal mock audits and ensure QMS adherence prior to CDSCO inspections.
Challenge 4: Query Resolution Delays
- Solution: Respond promptly and thoroughly to queries with supporting evidence.
Expert Consultation and Support
Given the complexity of obtaining a Class D license for Polyglyconate sutures, expert consultation is invaluable. Our team has successfully guided over 500 manufacturers and importers through the CDSCO process, minimizing delays and ensuring compliance.
We offer:
- Gap analysis of your documentation and processes
- Preparation of Device and Plant Master Files
- Assistance with test license and product testing coordination
- Audit preparedness and support
- Liaison with CDSCO authorities
Getting Started with Your CDSCO License Application
Register on the CDSCO MD Online Portal: Begin by creating your company profile.
Initiate Test License Application (Form MD13): This is mandatory before full manufacturing license submission.
Coordinate Product Testing: Schedule testing with CDSCO-approved labs early to align timelines.
Prepare Documentation: Develop comprehensive DMF, PMF, and risk management files with expert input.
Plan for Audit: Ensure your manufacturing site and QMS are audit-ready.
Submit MD9 License Application (Form MD7): Once test license and testing are complete.
Engage with CDSCO: Promptly address any queries to avoid delays.
By following these steps carefully and leveraging experienced regulatory support, you can successfully obtain your CDSCO license for Polyglyconate sutures and confidently enter the Indian medical device market.
For personalized assistance, connect with us today to streamline your CDSCO licensing journey.